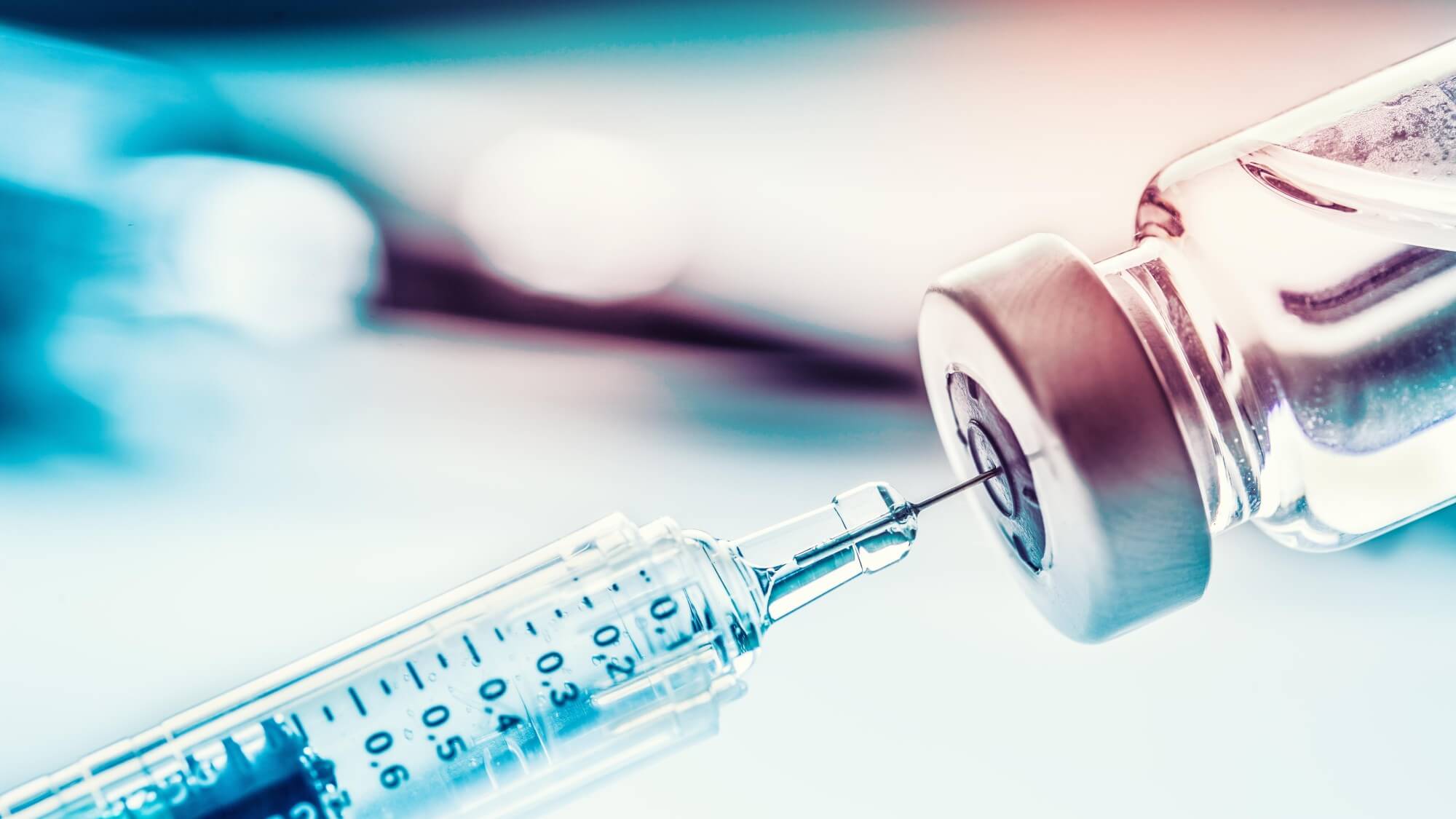
January 25, 2021
Your Ultimate Guide to Pharmaceutical Temperature Mapping
Drug manufacturers suffer billions of dollars in losses each year by failing to keep medicines and vaccines at correct temperatures. This does not even include costs for resupplying the drugs.
Temperatures can exceed recommended ranges anywhere along the supply chain. Proper pharmaceutical temperature mapping prevents these temperature fluctuations.
As a result, manufacturers save billions of dollars in ruined drugs. Stable temperatures ensure life-saving medicines get to the people who need them.
Your supply chain crosses continents. How can you maintain consistent temperatures? Do not fear—this guide serves as a resource for pharmaceutical temperature mapping.
Why Is Pharmaceutical Temperature Mapping So Crucial?
When pharmaceutical temperatures exceed their acceptable range, chemical properties change. This makes them less effective and sometimes renders them useless.
Mapping temperature readings at each step along the pharmaceutical’s journey is crucial. Proper storage and temperature mapping are even more critical for vaccines. This is because vaccines are especially fragile.
You can see this play out now with the COVID-19 vaccine. Manufacturers have to transport and store it at ultra-low temperatures.
Global investment in pharmaceutical cold chain storage confirms the importance of temperature mapping. Companies will spend more than $21 billion in cold chain services by 2024. This represents 24 percent growth over the next four years, according to the 2020 Biopharma Cold Chain Sourcebook.
This figure includes data services, such as using temperature sensors to track shipments along the entire chain.
The temperature mapping process can also prove that your pharmaceuticals are safe. This can actually lead to increased sales and profits.
Mapping Areas to Monitor
The first step in the storage temperature mapping process is to determine what areas of each storage system need monitoring.
Temperature sensors have to be positioned throughout a cold storage system for accurate data. Mapping out the placement of these sensors is key to maintaining consistent temperatures.
The temperature differences in cold storage areas can be as great as 10 degrees Celsius. The center part of any storage area will maintain the most consistent temperature. Temperatures will fluctuate more in corners and areas with increased air circulation.
Factors Affecting Area Mapping
When you conduct temperature mapping, you must also consider variables that impact these storage systems:
- changing climates
- areas with direct sunlight for an extended period
- areas with restricted airflow
- open windows and doors
- heating and air conditioning (HVAC) systems
Special Cases in Temperature Mapping
Warehouses need specific attention because of their external walls. You might have to map these areas over an entire year to account for seasonal factors. This data will inform where to place the permanent monitoring systems.
Cold rooms and refrigerators might only need to be mapped once. They typically are not affected by external factors. If the storage unit sits inside a warehouse, you should test it during the warehouse’s most extreme periods.
Determining the Proper Equipment to Use
The equipment you use in the temperature mapping process will vary in accuracy. It will also vary in response time to temperature changes.
If you choose to install budget equipment, check the accuracy ratings first. The best equipment will provide accuracy within 0.3 degrees Celsius. Cheaper alternatives might only be accurate to within a degree.
You should install backup systems to ensure that monitoring continues under extreme circumstances.
Testing the Load of the Facility
The second critical factor in pharmaceutical temperature mapping is load testing. Load testing measures what impact the temperature-controlled storage systems have on pharmaceuticals.
When you test a cold storage facility’s load, you have to consider whether the drugs need cooling when they arrive. Cooling the shipment to the proper temperature will have a drastic effect on the temperature of the storage facility.
In addition to load testing, all monitoring systems should be evaluated with simulated failures. This will determine if the system remains functional even if some equipment breaks down.
Installing Your System
After you have temperature-mapped your system, you can begin installing sensors.
Place sensors in areas most prone to changing temperatures. You should also watch the stable areas. This will help you troubleshoot problems if they occur.
Sensors should be installed near pharmaceutical products. You should place sensors at different heights and near doors and ceiling fans. These are places where temperatures will fluctuate.
You should also be aware that different countries establish different standards. Your layout will depend on local guidelines as far as the total number of sensors to hook up.
Ensuring Accuracy
You can arrange monitoring equipment in zones. The zones can be based on areas influenced by similar factors. As an example, you will see similar readings from each corner of a storage facility. You will also see similar patterns in zones near windows, doors, or HVAC units.
To achieve the most accurate readings, you should install sensors in “thermal lags.” They mimic the effect of product packaging. The thermal lag, a container of thermal fluid like glycol, dampens the sensor’s reaction to occasional temperature spikes.
Once you install sensors, you can start recording temperature fluctuations. Be sure to note the high and low temperatures that occur in your mapped area.
Ongoing Maintenance
The work you put into temperature mapping will go to waste if you do not maintain the system. You must create a schedule for maintenance and routine calibration. This will help your system maintain consistent readings.
You should calibrate equipment at least once a year. You need to document all maintenance and calibration procedures.
Reliable Options for Obtaining Quality Data
You can start collecting real-time data after you map your system and install sensors. This will give you confidence that your pharmaceuticals are safe.
To outfit your system, choose the products that the FDA trusts and uses to monitor its labs. SensoScientific’s temperature monitoring products enable you to perform accurate pharmaceutical temperature mapping. They can also help you obtain consistent quality data.
SensoScientific provides quality products to meet needs in the healthcare industry. If you want to know how one of our products can help you, reach out to one of our experts today.