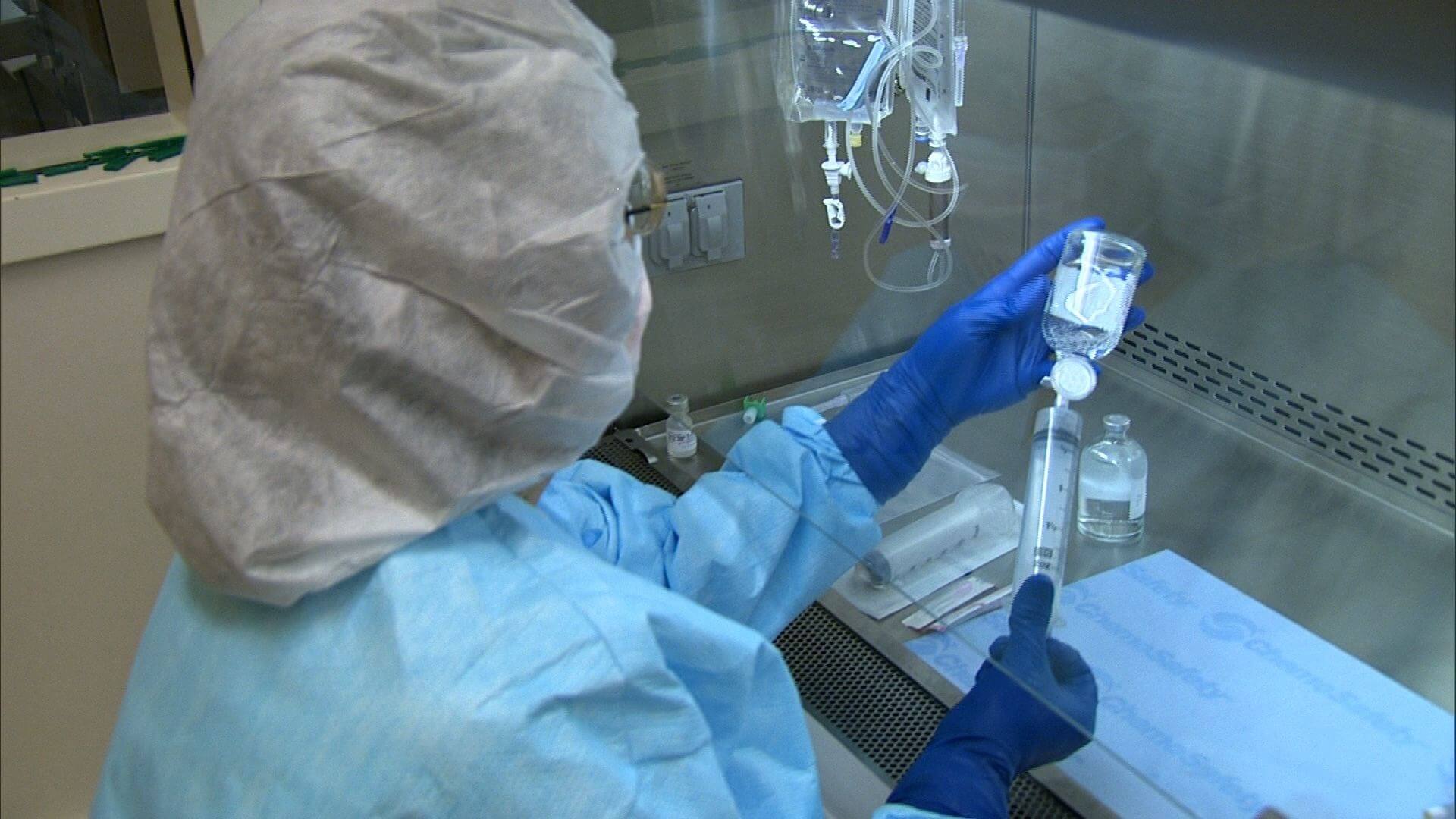
February 27, 2020
Differential Pressure Monitoring Systems for Pharmaceutical Compounding
Even today, asking a layman about how chemists operate, particularly in the form of pharma-tech, conjures a particular image to mind. That is the image of a lone scientist working in a room laden with colorful bubbling liquids. A fizz and hiss of substances crackling with exothermic reactions as ‘science’ get made.
To be fair to the popular mythos behind research labs, the effects are all wrong but the idea of a lone person toiling in a room is not. When it comes to pharmacy compounding, you need tight controls. These keep reactions stable and predictable.
Even a quick perusal of a cleanroom’s design requirements shows how much thought and study goes into these rooms. Crafting rooms that allow tight control of internal conditions takes engineering know-how.
Many conditions get considered in compounding. This guide explains the role of differential pressure on compounding tasks.
Pharmacy Compounding Standards
The United States Pharmacopeia (USP) is the governing body for compounding standards. They set out revisions to necessary conditions and safety equipment. These standards differ from FDA requirements due to the difficult tasks of pharmaceutical compounding.
Unlike other pharmaceutical manufacturing, compounding has a wider margin for error. It has to, as it accommodates individualization for particular patients. However, the emphasis remains on tight controls and safety standards.
The purpose of a compounding pharmacy is to create a useful, and safe, drug in a variation not commonly available. This can be performed for a variety of co-indicated health concerns. A patient may be allergic to a binder or dye in a typical formulation. Sometimes it is necessary to alter the compound from a liquid to a solid or vice versa.
The FDA cannot verify the efficacy or safety of a hand-made compound. For this reason, compounding pharmacies have developed and followed their own standards. This is when the UPS overlaps to cover these necessary tweaks.
Risks
Compounding comes with a set of risks linked to the complex interaction of each of the active ingredients. The various stabilizers and binders were added to create the compound interaction.
The compounding pharmacist isn’t working in completely unknown territory when making these changes. The conditions under which they work come designed to limit undesired effects. Any compounding comes with the possibility of cross-contamination and unstable interactions.
However, they are working with a sliding scale of parameters and conditions. A typical pharma-grade substance has precise controls placed after extensive testing. These conditions need monitoring within a tight error tolerance.
A compounding pharmacy, by need, makes changes to the environment and conditions to process each substance. This also requires considerable monitoring to prevent issues. The monitoring has both a wider error margin to encompass other reactants and compounds at use.
Differential Pressure Monitoring
The pressure difference between the cleanroom and the compounding chamber makes all the difference in this type of work. As the difference between the two areas fluctuates, the component vapor pressures can fluctuate.
Unlike material solids, complex organic molecules deteriorate rapidly outside of specific vapor pressures. In compounding, you seek to retain the efficacy of substances. While undesired effects are a worry, loss of potency is the key concern.
The margin for error in complex organic molecules is tight. This isn’t surprising as many of these substances are highly reactive. Stability in structure and a high degree of reactivity aren’t often found together.
Our monitoring systems help to maintain the integrity of organic molecules. This and maintaining the sterile environment inside the chamber. The need for positive pressure to keep intruding elements out and chamber pressure specific is difficult, but not impossible.
Differential pressure monitoring, by definition, needs to occur in multiple places at once. There is no measuring the differential if you don’t measure external and internal conditions.
Through the use of compact pressure probes, monitoring conditions from multiple locations is simple, even in tight areas. Remote monitoring through Wi-Fi sends data sets to monitoring stations and devices. Data retrieval through mobile devices gives constant feedback.
Pressure Basics
The properties of pressure, driven by airflow, aren’t static. Fluctuations within the tolerance are not uncommon. To measure the differential pressure the sensors need calibration. This takes into account measuring independent routine changes in parameters.
A technician moving by the sensor should not affect it to measure a total pressure change for the system. Through the use of square root extraction and DCS systems, flow can be properly gauged to give accurate results.
The use of differential pressure transmitters is most common for evaluating conditions. These devices feed high and low-pressure samples into separate housings. Of course, these units tend to be bulky and don’t allow for the precise control of digital variants.
Cleanroom Basics
Pressure monitoring doesn’t only cover the work area and the surrounding room, but also the ante-chamber. If conditions in the airlock deteriorate, the resulting loss of positive pressure creates an avenue for infiltrates to accumulate.
Even if the pressure in the cleanroom never dips, problems begin. This loss within the ante-chamber accumulates elements that can be tracked or pushed into the work area over time.
Seals
Most modern cleanroom designs allow for reconfiguration. This is needed to accommodate constant changes in projects. Most often, the workable space changes as quantities and demand change.
Obviously, sterilization and restoration of clean conditions are paramount after a reconfigure. This includes adjustments to room monitoring and work areas.
It shouldn’t take any more work to accommodate a new configuration than simply resetting sensors. Ideally, moving the probes will recalibrate for the new space and return accurate measurements. After an adjustment period, the probes know what incidental factors to ignore.
However, any change to the configuration can leave unseen gaps in seals. It’s ideal to give a settling time after a reconfiguration to ensure that conditions are stable.
Test Better
A worker is only as good as the tools they have on hand. For the critical accuracy of differential pressure needed in pharmacy compounding, only the best tools will do. Contact us to learn more about our monitoring systems and the services we provide.